1.顾桥煤矿是淮南矿业集团实施“建大矿、办大电、做资本”发展战略,建设煤电一体化新型能源基地而首批开工建设的核心工程,建设规模年产1000万吨,是亚洲开采规模最大的矿井,被誉为“亚洲第一井架”。西门子控制系统应用后,业主认为明显降低了设备故障率、简化了操作、减轻了工人劳动强度、提高了生产运行的安全可靠性、最大限度地缩减装卸载的时间,达到了提高产量,实现增效的目的。
2.顾桥矿井主井深800米,井筒直径为7.5米。主井架高78.6米,重854吨,装备2套32吨箕斗,年最大提升能力1440万吨.井下每套装载系统对应三个40米原煤仓,仓下有六台给煤机,一条宽1.4米长60米的装载胶带机,胶带机对应一个32吨的定量斗,定量斗下有定量斗闸门和装煤分配器及舌板。卸载采用曲轨卸载方式。
3.整个系统使用315-2DP CPU模板 3个,PS307 电源模板 3个,32点DI 7个,32点DO 7个,8CH AI 2个,OLM 光纤链路模块 3个,CP5611 1个,WINCC RC1024 1套,CP342-5通讯模块 1个,CP343-1以太网模板 1个,MiniRanger Plus200 双点料位仪表 1个,XPS-15探头 2个,SITRANS LU02双点料位计 1个,XLT-60探头2个,SIWAREX U 称重模块 2个,CC-100T称重传感器 4个。
4.矿区图片
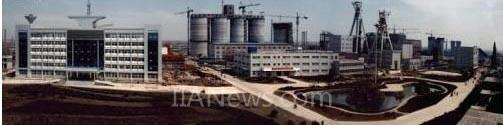
二、 控制系统构成
1. 系统结构图
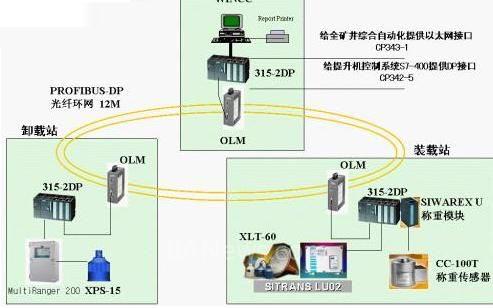
2. 系统软硬件配置
·在提升机房设S7-300 PLC主站,在卸载站设S7-300 PLC分站,在井下装载设S7-300 PLC分站。
·S7-300 PLC CPU 采用315-2DP ,主站和分站之间通过OLM组成PROFIBUS-DP工业光纤环网。
·提升机房还设上位机,通过CP5611与提升机房S7-300 PLC主站的MPI口连接,组态软件采用WINCC。
·提升机房S7-300 PLC主站的通讯模板CP342-5与提升机主PLC S7-400组成PROFIBUS-DP,通讯模板CP343-1提供给全矿井综合自动化以太网接口。
·在卸载煤仓和装载煤仓分别使用SIEMENS MiniRanger Plus短量程物位计和SITRANS LU长量程物位计。
·在井下定量仓采用CC系列柱式称重传感器及SIWAREX U 多功能的称重模块。
·在三个PLC站还设置DI 数字量输入模板、DO 数字量输出模板、及AI模拟量输入模板。
3. 软硬件选型依据:
·遵循“五高”建设方针,即高起点、高技术、高质量、高效率、高效益,突出效益优先;
·技术先进,可靠性高,扩展与升级容易,具有故障自诊断功能,做到够用、适用、好用、易扩展;
·网络通讯功能强大,易于与其它系统集成。
设备层选用SIEMENS 的超声波料位机,非接触式技术减少维护 、易于安装:使用可移动的红外编程器易于编程 、带背光的液晶显示器显示标准工程单位读数 。称重模块经过系统的集成,明显降低费用。增加精度及可靠性,系统更换无需重新标定,模块称重故障报警容易记录和监测。精度:0.05%具有65535分度分辨率 、无需调节重量能进行理论的调节 。
控制层选用S7-300 PLC 315-2DP通过OLM组成PROFIBUS-DP工业光纤环网。12M 的通信速率和可靠的通信质量、灵活的拓扑结构以及冗余的通信模型 、强大的通信功能,支持基于总线的驱动技术和符合IEC61508 的总线安全通信技术,是整个系统安全可靠运行的保证。
信息层选用SIEMENS工业以太网及WINCC组态软件,利用工业以太网,SIMATIC NET 提供了一个无缝集成到新的多媒体世界的途径,工业以太网技术上与IEEE802.3/802.3u兼容,使用ISO和TCP/IP 通讯协议。WinCC集生产自动化和过程自动化于一体,实现了相互之间的整合。
4. 方案比较:
与第一代继电器和集成电路同类产品和第二代PLC加传统简易传感器及进口的装卸载系统相比,此系统具有以下优势:
·整个系统有机的完美结合,所有数据信息均可通过软件分析及网络传输,是一套真正的全数字,全集成的系统。
·系统采用现场总线通讯的方式,减少了现场的布线。
·减少了系统的投资,增加了设备所带来的经济效益。
·缩短了系统现场的调试时间。
·增加了系统的安全性,可靠性,稳定性,先进性。
·给现场的工程师维护带来了极大的方便,减少了设备后期的服务。
三、 控制系统完成的功能:
1. 主要功能特点
☆ 主井提升信号及自动装卸载各自具有自动、手动、手动解锁三种工件方式,点动方式用于装卸载的调试和检修。信号在检修状态只有慢车信号。
☆ 自动装载定量、定容、定时保护及显示。
☆故障自动报警功能,及传感器的故障自诊断。
☆ 提升次数记忆功能和提升信号的断电记忆功能。
☆ 有工业光纤环网冗余通讯功能。
☆ 上、下井口信号间的闭锁功能、检测箕斗的装卸载位置异常功能
☆ 防止二次装载保护功能。
☆ 主井提升信号及自动装卸载有上位机系统、能监测各个设备的运行状态、故障记忆查询、产量的累计及报表、空载、满载、超载的标定,及定量斗假余煤的校零功能。
☆ 与绞车控制回路的闭锁功能、及PROFIBUS-DP软件通讯回路闭锁。
☆ 有联络呼叫功能。
☆ 有井上下煤仓煤位的连续实时监测功能。
☆ 有与全矿井综合自动化的以太网接口。
☆ 系统有供电电源的绝缘监测与电压监测功能。
☆ 有箕斗的卸载状态监视功能,检测箕斗是否卸空。
☆ 有对装载皮带的温度、烟雾、跑偏、堆煤、断带及拉线急停的保护功能。
☆ 有对动力负荷的保护上位机监测功能,如缺相,短路,堵转,过载,相不平衡,漏电等故障进行监测保护。
☆ 整个系统的通过网络访问维护功能。
2. 系统工作流程图与系统工作原理
系统工作流程图
◇ 井下信号、装载系统自动方式:以A箕斗为例,B箕斗与其操作相同。
*注:按装载急停按钮,可使装载站设备在任何状态下停止输出。按下信号急停可使提升机在任何状态下停止运行,信号闭锁在箕斗到位状态下按下,可防止提升机启动。
自动装载的顺序是:箕斗到位后,箕斗到位传感器自动发出停车信号,定量斗闸门打开,装载控制台显示屏上的闸门开灯亮。定量斗开始向箕斗装煤,等到显示屏上“定量斗满载”LED显示熄灭, “定量斗空载”LED显示点亮,,PLC自动关闭闸门。等到显示屏上的闸门灯亮,信号自动发出,(使皮带向定量斗装煤)同时启动皮带机,再经过一段时间延时,等到皮带机正常运转后,启动给煤机开始向定量斗装煤,此时称重显示瞬时值,等到显示屏上出现“满载”LED 显示,自动停止给煤机,皮带机运转,为下一勾提升作准备。当装载过程中出现特殊情况时,可按下装载部分的急停按钮,整个装载部分设备将全部停止工作,等到故障处理完后再进行工作。
3. 系统中的控制难点:
·整个系统中三个站PLC通讯控制的连贯性,因为整个装卸载系统的每个循环周期必须达到设计时的23秒钟内,所以系统在软件上,PLC间的通讯及称重的实时运算必须紧密的结合,各个控制部分必须全集成,否则提升周期很难保证,无法保证设计提升产量。
·动态称重监测控制:因为在一个定量斗下设置了4台称重传感器,所以必须要到PLC做定量斗的去皮,及空载、满载、超载的运算及设定。PLC对高精度称重模块进行现场控制,从高精度称重模块取得现场高精度的称重值,进行自动称量操作,并向称重模块发出各种控制指令。PLC与称重控制及判断过程状态,形成一个闭环控制系统,实现生产的高度自动化。
·超声波料位控制系统:针对井上煤仓仓体小10米,物料变化快及井下原煤仓仓体大40米,原煤粉尘严重的特点,选择安装位置十分重要,避开下料孔,计算超声波探头的发射角,使用Dolphin Plus 软件分析回波情况,找到最佳探测点是系统稳定可靠的难点。
·防止箕斗提升的超载及二次装载问题,利用高精度的称重模块及与PLC的运算、闭锁逻辑。利用PLC中的DB数据块的掉电记忆功能,即使是在任何情况下都不能使提升机超载提升,防止提升事故的发生。
·上位机WICC 系统通过ODBC接口在报表中打印Microsoft Access数据库中的数据,及WICC的集成诊断功能。
4. 部分画面照片:
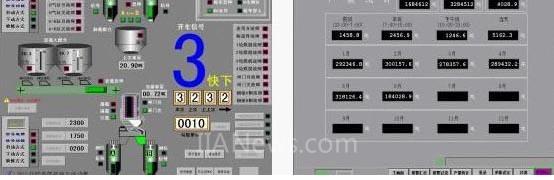
四、 项目运行:
2006年4月份系统软硬件调试完成,正式投入使用至今,设备运转情况良好,未出现任何故障,得到了用户的认可和好评。由此可以证实,系统的设计、选型是合理的,系统的运行是可靠的,系统的技术及检测手段是先进的,达到了最初的设计要求。
五、 应用体会:
这个系统在应用中的最大特点就是它的全集成特性、产品的可靠性及技术的先进性。全集成(TIA)使得项目的调试,软件的编程,硬件的接口,变得容易,省掉了近一半的工时。由于它的高可靠性使其成为煤矿咽喉一样的主井提升信号及自动装卸载控制的首选产品。由于它的技术先进性使得整个项目减少了现场的布线,减少了维护量,井下工人的减少,保障了矿井的安全高效运行。
(转载)