数控机床是现代制造业的关键装备,一个国家数控机床的产量和技术水平在某种程度上就代表这个国家的制造业水平和竞争力。我国数控机床的技术水平、性能和质量与国外产品比较还有很大差距。高性能加工中心和功能部件大多数依靠进口。加工中心是数控技术的集中体现,市场活跃、需求旺盛,成为当前和未来数控机床市场争夺的前沿。
加工中心是备有刀库并能自动更换刀具,对工件进行多工序加工的数字控制机床。工件经一次装夹后,数字控制系统能控制机床按不同工序,自动选择和更换刀具,自动改变机床主轴转速、进给量和刀具相对工件的运动轨迹及其他辅助机能,依次完成工件几个面上多工序的加工。加工中心由于工序的集中和自动换刀,减少了工件的装夹、测量和机床调整等时间,使机床的切削时间达到机床开动时间的8O%左右(普通机床仅为15~20%);同时也减少了工序之间的工件周转、搬运和存放时间,缩短了生产周期,具有明显的经济效益。加工中心适用于零件形状比较复杂、精度要求较高、产品更换频繁的中小批量生产。 第一台加工中心是1958年由美国卡尼-特雷克公司首先研制成功的。它在数控卧式镗铣床的基础上增加了自动换刀装置,从而实现了工件一次装夹后即可进行铣削、钻削、镗削、铰削和攻丝等多种工序的集中加工。二十世纪70年代以来,加工中心得到迅速发展,出现了可换主轴箱加工中心,它备有多个可以自动更换的装有刀具的多轴主轴箱,能对工件同时进行多孔加工。这种多工序集中加工的形式也扩展到了其他类型数控机床,例如车削中心,它是在数控车床上配置多个自动换刀装置,能控制三个以上的坐标,除车削外,主轴可以停转或分度,而由刀具旋转进行铣削、钻削、铰孔和攻丝等工序,适 于加工复杂的旋转体零件。加工中心按主轴的布置方式分为立式和卧式两类。卧式加工中心一般具有分度转台或数控转台,可加工工件的各个侧面;也可作多个坐标的联合运动,以便加工复杂的空间曲面。立式加工中心一般不带转台,仅作顶面加工。此外,还有带立、卧两个主轴的复合式加工中心,和主轴能调整成卧轴或立轴的立卧可调式加工中心,它们能对工件进行五个面的加工。加工中心的自动换刀装置由存放刀具的刀库和换刀机构组成。刀库种类很多,常见的有盘式和链式两类。链式刀库存放刀具的容量较大。换刀机构在机床主轴与刀库之间交换刀具,常见的为机械手;也有不带机械手而由主轴直接与刀库交换刀具的,称无臂式换刀装置。为了进一步缩短非切削时间,有的加工中心配有两个自动交换工件的托板。一个装着工件在工作台上加工,另一个则在工作台外装卸工件。机床完成加工循环后自动交换托板,使装卸工件与切削加工的时间相重合。
2 数控机床主轴驱动
主轴驱动系统是数控机床的大功率执行机构,其功能是接受数控系统(CNC)的S码速度指令及M码辅助功能指令,驱动主轴进行切削加工。主轴的驱动可以使用交流变频或交流伺服2种控制方式,一般的交流变频主轴能够无级变速但不能准停,需要另外装设主轴位置传感器,配合CNC系统PMC (指数控系统内置PLC)的逻辑程序来完成准停速度控制和定位停止;交流伺服主轴本身即具有准停功能,其自身的轴控PLC信号可直接连接至CNC系统的PMC,配合简捷的PMC逻辑程序即可完成准停定位控制,且后者的控制精度远远高于前者,所以目前大多数加工中心的主轴驱动系统采取交流伺服主轴。参考交流伺服主轴的功能,台达公司开发出新一代的交流变频驱动器——VE变频器,除了功能和性能完全能够和交流伺服媲美,而且还具有通用性强以及价格上的优势,通过多次测试深得客户的认可与喜爱。
3 台达VE变频主轴驱动系统
3.1 系统设计要求
(1)VE系列变频器功能和性能的数控特性。项目客户为数控加工中心知名企业。结合客户的要求以及加工中心的特性,台达专门为数控加工中心开发的高性能变频器————VE系列变频器功能和性能是非常适合使用在数控加工中心上的:
•通过外部I/O点能够实现快速单点定位,有专门参数调整定位时的特性曲线以及定位时间,定为实现方便;
•通过专用参数调整达到快速加减速的实现;
•全新的PDFF控制,使增益的调整更加简单方便,易于掌握;
•接受模拟量信号和脉冲信号,对上位机的支持更加全面。
(2)测试加工中心配置:
•数控系统:台湾新代数控系统SYNTEC 9401;
•主轴规格:无锡博华电机8kw/最大频率600hz-12000rpm/6P/380V/450hz/25A,编码器+5V/GND/+A/-A/+B/-B/+Z/-Z/512ppr;
•变频器规格:075V43A-2+EMV-PG01L,软件版本9.98测试版,制动电阻1500W/75ohm。
3.2 主轴变频系统设计
(1)变频器电气设计:参见图1。
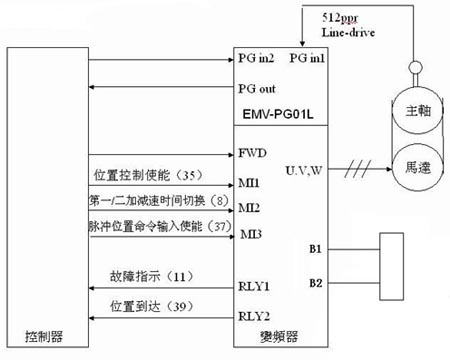
图1 变频器配线图
3.3 变频器参数设计步骤
(1)将电机参数设置到变频器,作电机动态自整定。要想将VE系列变频器的高性能发挥出来,准确的电机参数是基础。首先将基本参数填入到变频器相关位置:
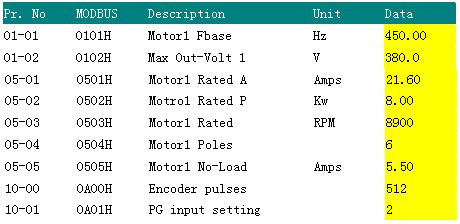
并且使用以上参数作VF控制运行,具体情况如下表,观察后符合电机运行特性。
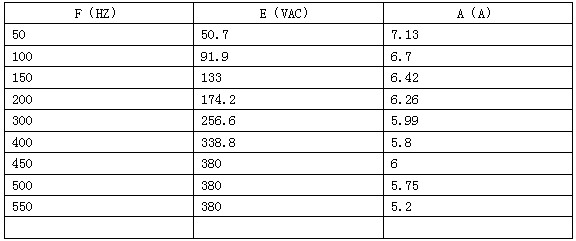
(2)解决一个有趣的工程问题。在以上数据中,电机额定转速05-03是电机厂家铭牌没有提供,询问电机厂家也不是很清楚。这种情况下,由于电机本身带编码器,通过VF控制,将变频器运行到450hz,观察变频器中提供的r状态,电机实际转速为8900rpm左右,将测的数据填入到05-03。电机额定电流25A,075V43A-2变频器额定电流只有18A,所以只能将电动机额定电流尽可能的调整到最大(最大为21.6A)填入05-01参数。
将参数5-00=1,然后按面板”RUN”作动态整定。
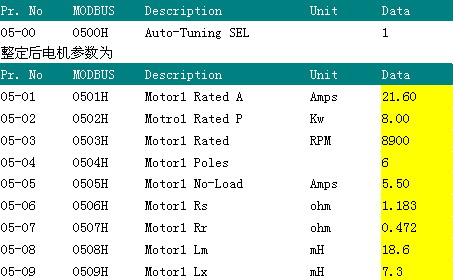
11-01参数关系到编码器方向的选择,如果设置不当,则PG闭环控制会出现问题。11-01设置是否正确可以通过在变频器面板r状态的观察,r如果是正值则表示方向设置正确,如果是负值则表示方向设置相反。
(3)将控制方式改为foc+pg,并且调整最大操作频率以及加减速时间
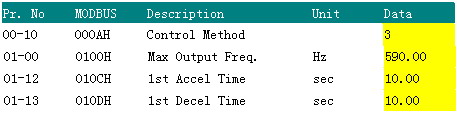
使用面板运行。首先将F=550,运行后发现不论启动过程还是停止过程,当输出频率到达450HZ左右时就不按照加减速时间来变化,变化非常缓慢。当出现以上现象时,可以通过调整参数11-05(M1IdsRef Limit)来解决,将11-05从出厂值90改为110后加减速过程正常。
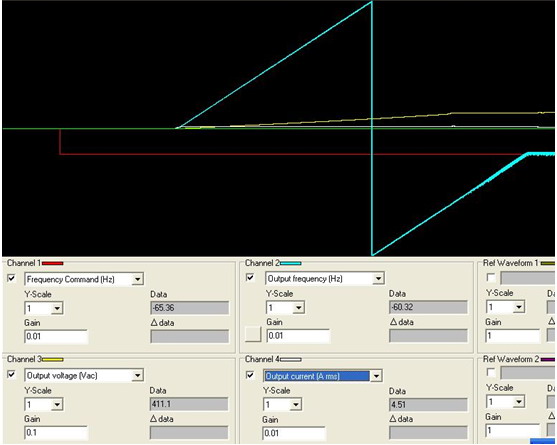
图2(F=590,11-05=180)加速曲线
(4)作惯量估测以及ASR自动调整。将参数11-00=2,F=200HZ,01-12=01-13=1,正反转后测得惯量参数为49,之后将11-01=1,观察电机刚性,并对相应参数作修改。
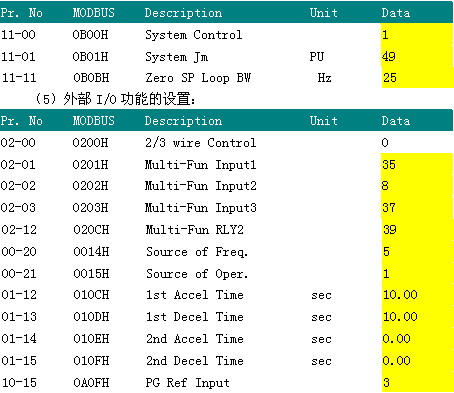
参见图1,MI1为单点定位,MI2为第一/第二加减速时间切换,MI3为脉冲位置命令输入使能做单点定位时,FWD/MI1闭合,变频器做定位动作。有如下参数对定位的灵敏程度以及定位时停止位置有关系,调整位置时可以将主轴停止在需要定位的位置并且观察面板上的G状态值,确定位置正确后将观察到得G值填入到10-19中;定位过程的灵敏程度通过调整10-21/10-22来改变,10-21越大,10-22越小,反映越快,定位过程越短;10-21越小,10-22越大,反映越慢,定位过程也越长。
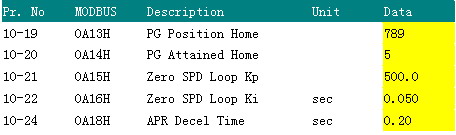
目前脉冲控制提供两种模式:速度模式以及位置模式。当工作在速度模式下,只需要将频率来源信号设置为脉冲给定,并且按照上位机提供的脉冲信号设置给定方式;如果变频器需要工作在脉冲位置命令模式,除了速度模式下的参数需要设置外,还需要配合外部端子信号FWD/MI1/MI2/MI3的闭合。
3.4 VE系列变频器脉冲输入控制
VE系列变频器支持两种脉冲输入方式:1.A/B相脉冲输入;2.脉冲+方向输入。由于新系统提供脉冲+方向的输出方式,所以可以选择如图3中第3种或者第4种方式;然后再根据方向来作出最后正确的选择。
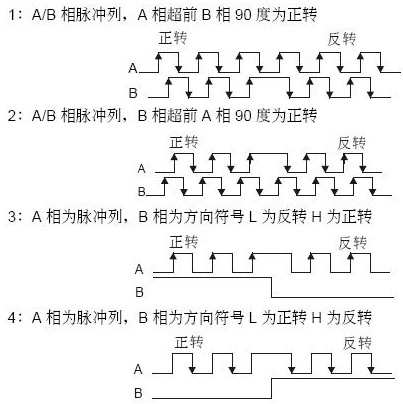
图3 接受的脉冲输入方式
使用脉冲控制时,还有两个参数也是非常重要的:1.10-17PG电子齿轮A;2.10-18PG电子齿轮B。其计算公式为转速=脉冲频率/编码器的点数(10-00)*电子齿轮A/电子齿轮B。
3.5加减速特性
加减速特性的测试,首先将保护功能作适当调整:

从0加速到590hz的加速过程中实测加速时间为1.4s,加速中最大电流为19.3A,图形参见图4。
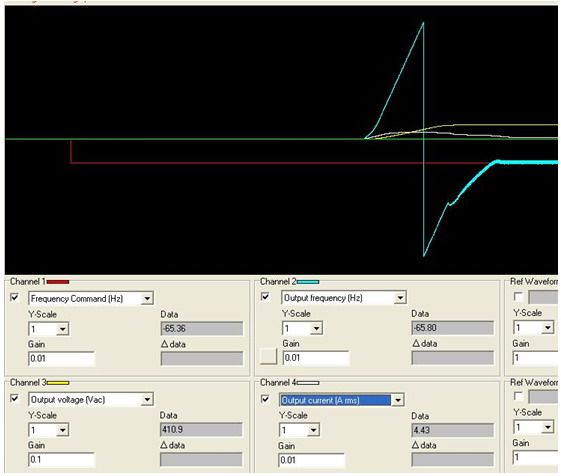
图4 加速曲线
1-12=5,1-13=5,F=590
从590hz减速到0hz的减速过程中实测减速时间为5.1s,减速中最大母线电压为740VDC,图形如图5所示。
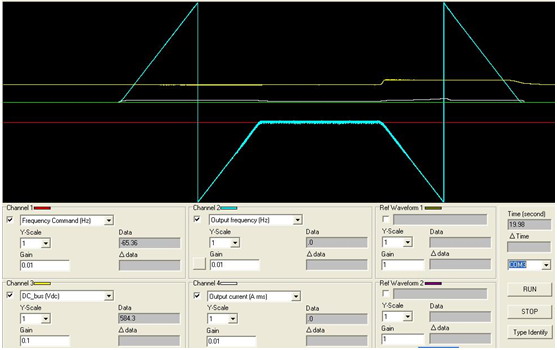
图5 加速以及减速曲线
4 结束语
数控加工中心对主轴有较高的控制要求,首先要求在大力矩、强过载能力的基础上实现宽范围无级变速,其次要求在自动换刀动作中实现定角度停止(即准停),这使加工中心主轴驱动系统比一般的变频调速系统或小功率交流伺服系统在电路设计和运行参数整定上具有更大的难度。基于台达VE系列高性能变频器的数控主轴变频驱动项目加减速特性以及定位功能都完全能够适应加工中心的要求,性价比突出。
(转载)