要感应这些独特的特性,需要有一台像罗斯蒙特 3051S 压力变送器一样具有快速传感功能的仪表,它的诊断特性板(图 1)中内置有我们的专利软件,可以计算噪音或变化的特性与数量统计参数。这些统计参数都是输入压力的均值和标准差。过滤功能的作用是将过程中的缓慢变化(一般由调整点变化引起)从相关过程噪音或变化中剔除出来。图 2 的例子为,在均值保持不变的情况下,噪音级的变化对标准差值会产生何种影响。
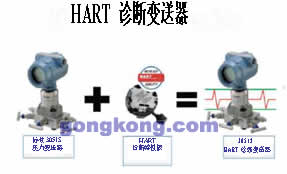
图 1:具有先进诊断功能的 3051S HART 压力变送器的结构
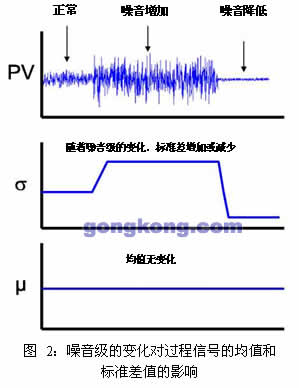
图 2:噪音级的变化对过程信号的均值和标准差值的影响
仪表的快速性和统计参数的内部计算尤为关键。速度较慢的仪表无法捕获过程或系统的噪音特性。由于这些仪表一般用于过程控制,所以出于此种目的,设备、集散控制系统或 PLC 中通常会采用各种形式的衰减或过滤措施,以降低过程信号中的噪音。这种过滤或衰减消除或显著降低了噪音信号。另外,考虑到带宽限制和典型 DCS 或 PLC 的取样率,在系统层面上对统计参数进行计算是不现实的。这些典型设备的信号取样率一般为每秒一次或者更低,这一速度远远及不上仪表对过程变量的取样速度(3051S 压力变送器的取样率则为每秒 22 次)。
罗斯蒙特仪表内,统计参数计算所占用的程序通道与过滤并计算一次输出信号(如 4-20 mA 信号)的程序通道并行。一次输出信号在任何情况下都不会受到这一附加功能的影响。
仪表可以通过两种方式向用户提供诊断信息。第一种方式:可以通过 HART 通信协议将统计参数传输到主机系统。使用这些统计参数,系统可以检测或显示过程环境下的变化。例如,统计数值被储存在 DCS 历史数据中。如果发生过程紊乱的情况,系统将检查这些数值,确定这些数值变化是否预示或指示了过程紊乱。之后系统将把这些数据直接显示给操作人员,或作出报警、警告指示。
第二种方式:仪表的内部程序通过学习过程确定过程噪音或特性的基准。学习过程完成后,仪表就可以独立进行检测,以确定噪音或特性是否发生了显著变化。它将通过 LCD 输出该事件,通过 4-20 mA 输出报警,和/或通过 HART 输出警告。
运行
图 3 是统计过程监控(SPM)诊断的简图。压力过程变量被输入到一个模块中,该模块会对压力信号进行高通过滤。以未过滤的压力信号为基础计算均值,以过滤后的压力信号为基础计算标准差。通过 HART 和通信手操器(如 375 现场通信器)或资产管理软件设备(如艾默生过程管理研发的 AMS™ 设备管理器)传输这些统计数值。
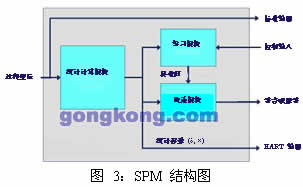
图 3:SPM 结构图
通过其它工具(如罗斯蒙特 333 HART Tri-loop)还可以在设备中进行非主要变量的赋值,并将这些数值传输给用户。
SPM 还包括一个学习模块,它可以为过程建立一系列的基准值。在那些被认为是正常的过程或安装情况下,用户通过 HART 监控并完成基准值的建立。这些基准值被传输到决策模块,与最新计算出的均值和标准差进行比较。用户通过控制输入功能选择灵敏度设置和动作,当设备检测到上述数值的显著变化时,SPM 诊断功能就会发出报警、警告,或采取其它行动。
图 4 是一个流程图,它对 SPM 诊断的运行进行了更详尽的说明。它是一个经过简化的流程图,说明了使用默认值的运行情况。当诊断程序不间断地计算均值和标准差时,必须将学习和决策模块激活为运行状态。一旦激活,SPM 将进入学习/检测模式。诊断程序将在用户设置的时间段内计算作为基准的均值和标准差(学习/监控期默认为 3 分钟)。诊断的状态将为“学习”。程序将进行一次检查,以保证过程具有足够高的噪音或变化级(必须高于变送器本身内部噪音的最低水平)。如果级别过低,诊断程序将继续计算基准值,直到满足标准为止(或程序被关闭)。通过检查后,程序将计算第二组数值,并将其与原来的那组数值进行比较,检验该测量过程是否具有稳定性和可重复性。在这一期间,诊断的模式将变为“检测”。如果过程稳定,诊断程序将把最后一组数值作为基准值,并切换到“监控”模式。如果过程不稳定,诊断程序则会继续进行检测,直至稳定为止。稳定标准由用户自定义。
进入“监控”模式后,程序将不断地计算新的均值和标准差,每秒就会有新数值被计算出来。

图 4:SPM 运行的简化流程图
新计算出来的均值将与基准均值进行比较。如果均值存在显著变化,诊断程序将自动返回到学习模式。之所以这样做,是因为均值的显著变化往往是由过程运行变化所引起的,在这种情况下噪音级(即标准差)也会因此发生显著变化.如果均值没有变化,程序将会对新计算出的标准差值与基准标准差进行比较。如果标准差与基准值相比有显著变化,超过了灵敏度的预设值,则说明过程、设备或变送器中发生了变化,程序将通过 HART 发出警告。
诊断出现故障时,仪表内的计时器也会对事件加以时间纪录。事件发生后,计时器会记录下经过的时间,以便用户能够将来自 3051S 的诊断显示信息与工厂内其它事件联系起来。计时器还记录仪表的总运行时间。这些时间值储存在诊断特性板的非易失性存储器中。
具有先进诊断功能的 3051S HART 压力变送器充分利用了最新的增强型 EDDL 技术,对通信手操器和基于 PC 平台的控制系统组态器(如艾默生过程管理研发的 AMS 设备管理器)的用户接口进行了优化。图 5 是 AMS™ 设备管理器显示的 SPM 诊断状态屏幕。该图中,红线表示均值和标准差的最新数值,蓝线表示它们的基准值,灰线表示灵敏度数值。这一屏幕还显示是否设置了警告、诊断模式、事件发生时的时间戳数值。在这个屏幕中可以对诊断进行开启/关闭操作,还可以用“Reset”(重置)或“Reset and Relearn”(重置并重新学习)命令清除已经显示的事件。其它可组态参数可在另外的屏幕中设置,并在产品说明手册中进行了详细说明。
SPM 应用举例
SPM 诊断可以用于各种压力测量领域。SPM 诊断在稳定的过程环境中能够发挥极大作用。在静态的运行环境下,如果噪音或特性发生变化,就说明过程、过程设备或变送器中将发生或已经发生了显著变化。

图 5:AMS 设备管理器增强型 EDDL SPM 状态屏幕
(在均值和标准差均可能发生显著变化的静态过程环境下,如液位测量环境,SPM 诊断也能够发挥它的作用,为您检测出一些问题。)下面是一些例子:
指示引压管线的阻塞
压力变送器一般通过小口径的管道与过程相连,这种管道叫做引压管线。在一些应用中,这种引压管线可能被固体物质堵住或由于气候寒冷而发生冻结堵塞,严重影响了压力信号的传递。通常情况下,用户无法获知这种情况。这是因为,堵塞发生时压力被阻挡,变送器所提供的信号与阻塞发生前它所提供的信号完全相同。只有当变送器输出未随着实际流量变化而变化时,才有可能发现管线堵塞问题。
用户可以对 SPM 诊断进行组态,使其具有检测引压管线堵塞的功能。.研究表明,在典型流量应用中,如果一条(DP 或 AP/GP 变送器)或两条引压管线发生堵塞,特定流量下标准差就会发生显著变化。(图 6)

图 6:引压管线发生堵塞
具体变化情况取决于多个因素,包括一次元件类型、引压管线的长度和规格、堵塞程度。
流体成分变化检测
研究表明,进行差压流量测量时,两相或多相流量情况下会比单相流量情况下产生更多不同的噪音形式,进而使差压信号的标准差也相应增加。SPM 诊断技术既可以对干燥气体中的大量液体变化进行检测,也可以对湿气中的液体显著变化进行检测。
试验表明,对于存在大量空气或其它气体的液体环境,SPM 诊断同样适用。
精炼炉火焰不稳检测
SPM 诊断的另一个应用例子是精炼炉火焰不稳检测。精炼炉经常焚烧各种具有不同 BTU 的废气。由于多种 BTU 共存,火焰很可能会变得不稳定,这将是精炼炉熄火的一个预兆。操作人员则希望尽量避免这种不稳情况的发生。在一家主要的精炼炉制造厂中进行了多次试验。火焰不稳情况出现(图 7)。通过对通风压力变送器监控火室内的压力的噪音进行过滤和测量,SPM 诊断技术可以检测出火焰不稳情况(图 8)。在精炼炉熄火前检测到异常,用户会有更充足的时间进行过程纠正。
注释:罗斯蒙特 3051S HART 压力变送器中的统计过程监控诊断功能可以计算并检测压力输入信号统计参数的显著变化。这些统计参数与压力信号中的噪音信号及其变化有关。但是,压力测量的实际应用环境下到底存在哪些噪音源,这些噪音源对统计参数具体有什么影响,噪音源随时会发生什么变化,则是很难精确预测到的。所以,艾默生过程管理无法绝对地保证,统计过程监控诊断功能在所有环境下都能对具体情况进行精确检测。
结论
在如何降低维护成本、提高维护质量、增加过程正常运行时间的问题上,过程、仪表和维护工程师面临着巨大的挑战。艾默生过程管理现在向您推荐用于罗斯蒙特 3051S HART 压力变送器的 ASP™ 诊断套件。这一套件具有先进的诊断功能和统计过程监控功能,帮助用户定位那些需要维护的设备,识别那些运行效率低下的设备,降低过程停机时间。

图 7:精炼炉和试验期间(包括火焰不稳的时间)的火室压力信号
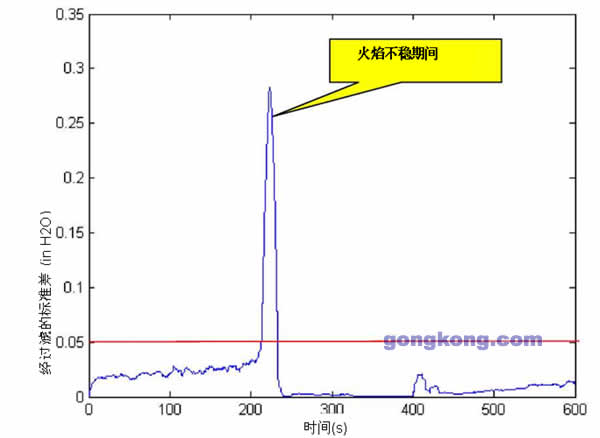
图 8:经具有先进诊断功能的 3051S HART 压力变送器过滤后,火室通风压力信号的标准差
(转载《》中国工控网)